Repenser l’automatisation
Dans le cadre d’un “projet interne, Cutmetall Recycling Tools Germany a entrepris d’acquérir des connaissances pratiques sur l’automatisation en un temps record. Leurs principaux partenaires : Fastems, Heller et Haimer.
L’objectif de ce projet était de développer et de tester de nouvelles normes de production, de nouveaux flux de travail, de montages et des programmes CN qui pourraient être directement transférés dans un système automatisé Fastems d’ici 2025. Ce faisant, Cutmetall a jeté les bases d’une montée en puissance rapide et peu risquée d’un système d’automatisation multi-machines.
Basée à Eisfeld, en Thuringe, Cutmetall Recycling Tools Germany fait partie du groupe Cutmetall et opère en tant qu’OEM avec environ 40 employés. L’entreprise fabrique des pièces d’usure et de rechange pour l’industrie du recyclage. “Nous produisons des lots de 1 à 20 000 pièces, la moyenne se situant entre 20 et 200 pièces”, explique Florian Fischer, directeur général.
Seul le ‘temps-copeaux’ génère des bénéfices –
il ne s’agit pas de faire tourner des machines pour le plaisir.
M. Fischer a un point de vue très particulier sur l’automatisation. Lorsqu’on lui demande comment il évaluerait le niveau d’automatisation de son usine avant le projet de Formule 1, sa réponse est claire : “Cela dépend de ce que vous entendez par automatisation. Nous disposons de 12 machines CNC, d’un centre d’usinage et de trois robots pour le chargement et le déchargement des machines. Cela peut sembler haut de gamme pour certains, mais pour moi, ce n’est pas le cas. Du point de vue de la production allégée, il y a encore trop peu de distinction entre la création de valeur et le gaspillage. L’automatisation ne devrait jamais avoir pour but de faire fonctionner les choses. Il s’agit de maximiser les heures de broche – c’est de là que vient le profit.
Apprendre rapidement de l’automatisation en situation réelle
Selon M. Fischer, la pénurie de travailleurs qualifiés est le principal obstacle à la capacité de production de Cutmetall. “Nous n’avions pas non plus d’équipement capable de fonctionner sans lumière et, jusqu’à présent, nous n’avions pas un seul centre d’usinage horizontal. Même sur les machines verticales, l’évacuation des copeaux est le principal goulot d’étranglement, ce qui rend difficile une production 24 heures sur 24 et 7 jours sur 7. En outre, nos machines ne disposaient pas de magasins d’outils suffisamment grands”.
Pour changer cela, Fischer et le copropriétaire Oliver Huther ont lancé le projet Formula 1, avec l’ambition de préparer un futur système multiniveau (MLS) de Fastems qui relierait plusieurs machines CNC dans un système de fabrication flexible. La première étape : mettre en œuvre rapidement une solution d’automatisation compacte et acquérir une expérience pratique précieuse.
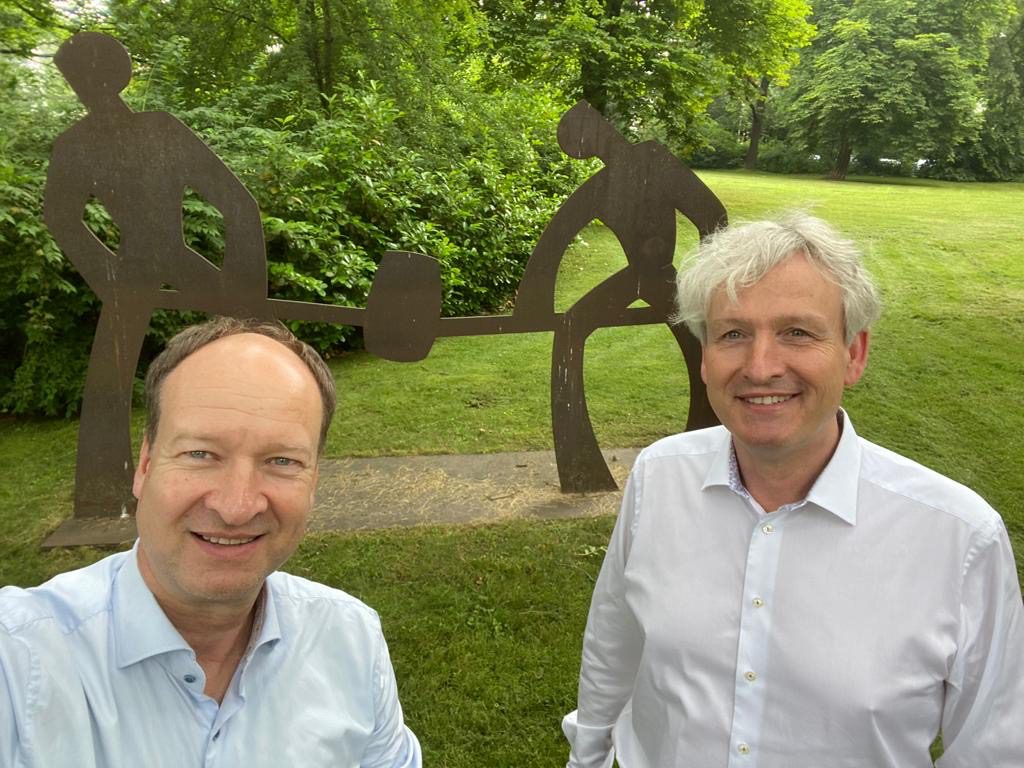
Les normes d’abord – comme fondement de la productivité
Pour soutenir cette transition, Cutmetall a commencé à normaliser systématiquement son environnement de production:
- Les investissements se limitent désormais aux machines avec la même CN , aux changeurs de palettes et aux systèmes de serrage.
- Seuls les centres d’usinage horizontaux dotés d’un système d’évacuation automatique des copeaux seront utilisés.
- La gestion des liquides de refroidissement et des lubrifiants sera également automatisée.
Fischer définit l’objectif principal comme suit : “Tous les processus de réglage, de changement, de manipulation des outils et d’enlèvement des copeaux doivent se dérouler parallèlement au temps d’usinage principal.”
Pour évaluer les partenaires potentiels en matière d’automatisation, M. Fischer a visité de nombreuses entreprises dans toute la région, dans le but d’apprendre des erreurs des autres avant de commettre les siennes.
Des progrès rapides :
Du salon AMB au système de production
Cutmetall a découvert le centre d’usinage horizontal à 5 axes HF 5500 de Heller à l’occasion du salon AMB 2022. Sur le stand de Fastems, ils ont découvert le palettiseur flexible (FPT) – la pièce manquante pour compléter leur solution.
“Peu après le salon, nous avons acheté le centre d’usinage directement sur la ligne de production de Heller, ainsi que le FPT-1000 de Fastems et un dispositif de préréglage de Haimer”, explique M. Fischer. “Nous voulions que l’ensemble du système soit opérationnel, entièrement intégré et productif, dès le mois d’avril de l’année suivante.
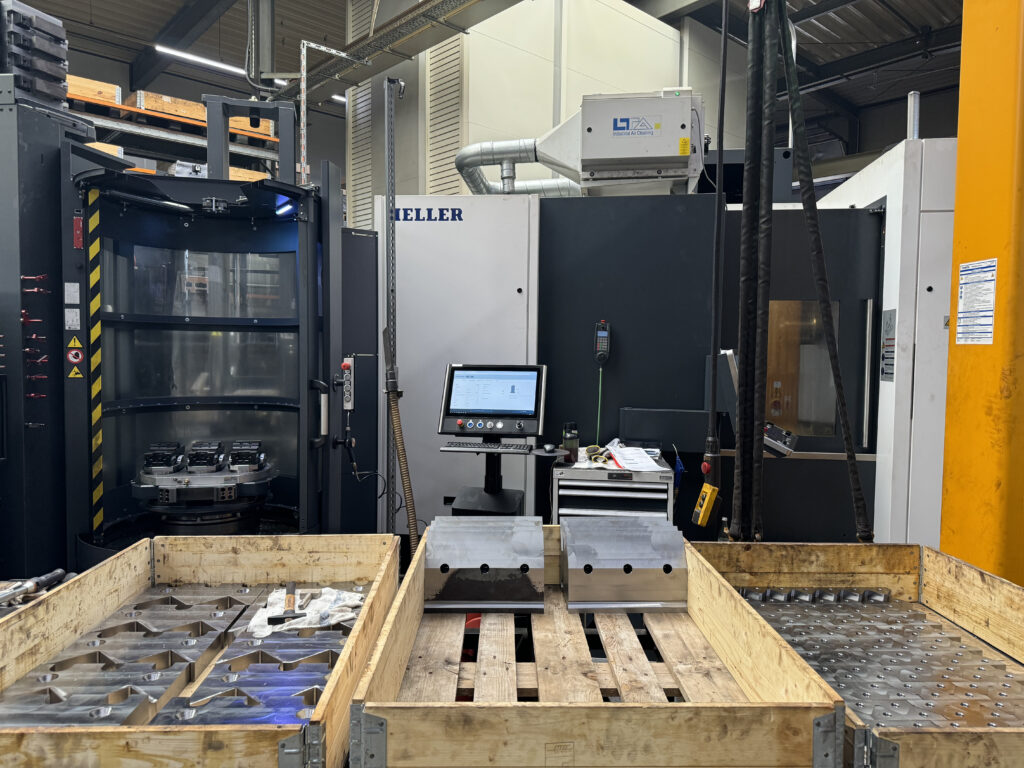
Ce qui a le plus convaincu M. Fischer, c’est le concept d’économie d’espace du FPT-1000, qui permet une grande capacité de stockage de palettes dans un espace compact. Conçu pour des charges utiles allant jusqu’à 1 000 kg (palette comprise) et des tailles de palettes comprises entre 500 x 500 mm et 630 x 630 mm, le système peut stocker de 12 à 24 palettes sur deux niveaux de hauteur, le tout sur une surface au sol de 19 m² seulement. Cette configuration permet une fabrication hautement productive, axée sur les commandes, avec une seule machine CNC.
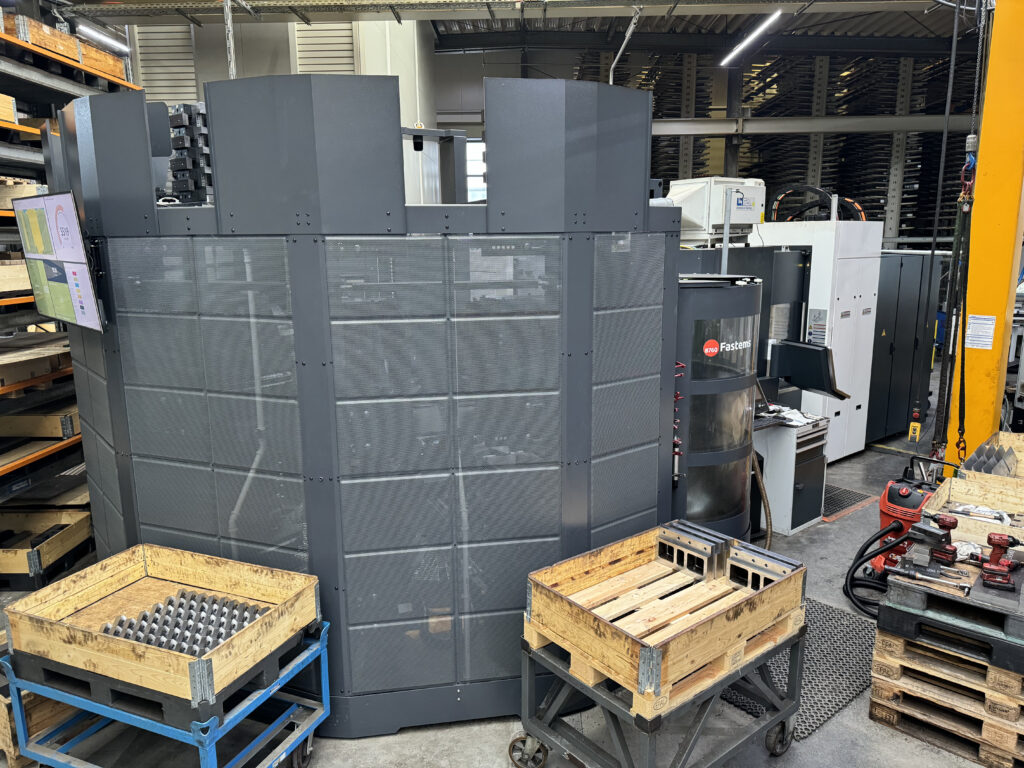
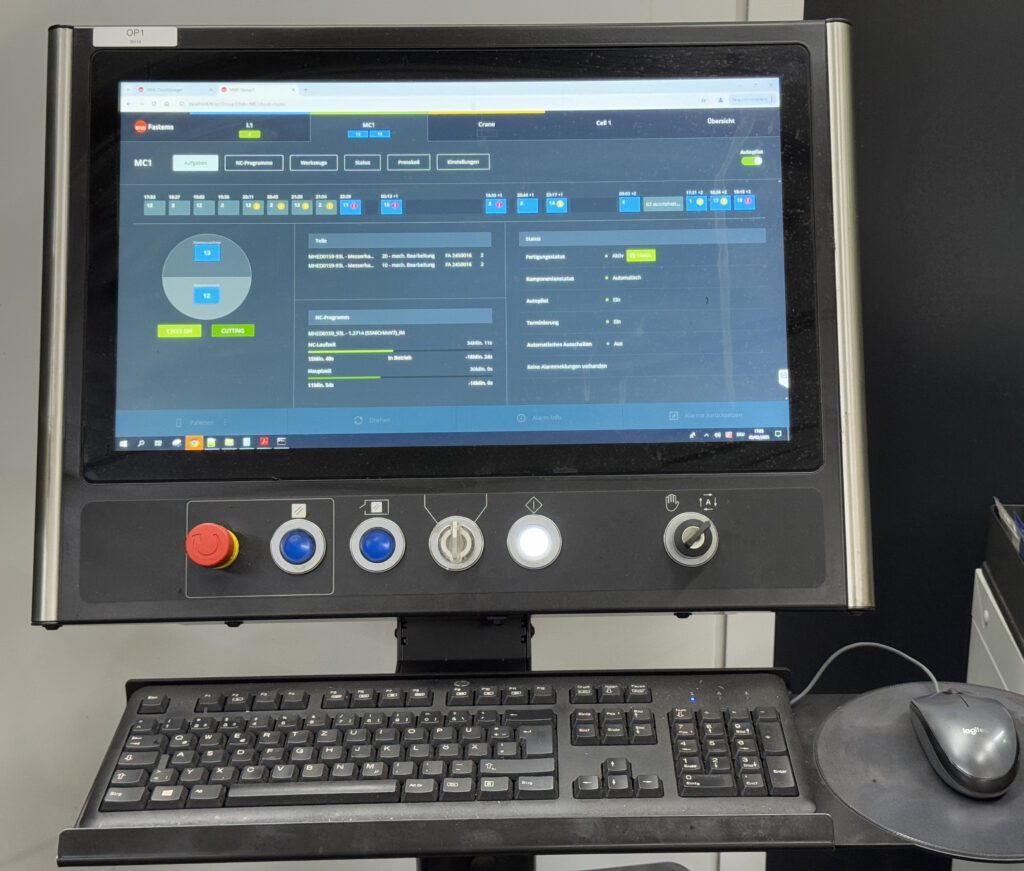
Pourquoi les logiciels ont fait la différence
Pour M. Fischer, ce n’est pas seulement le matériel qui a fait pencher la balance, mais l’intégration globale du système, et en particulier le logiciel. “Les interfaces logicielles entre la machine, le dispositif de préréglage et l’automatisation sont absolument essentielles. Le logiciel MMS (logiciel de gestion de la fabrication) de Fastems a finalement fait pencher la balance en faveur de Fastems.
Le MMS est l’une des solutions logicielles les plus avancées pour la planification, l’exécution et le suivi automatisés de la production. Il permet de planifier les opérations de fabrication jusqu’à 96 heures à l’avance. Plus important encore, il se concentre sur la préparation des ressources : “Avant le lancement d’une tâche, le MMS vérifie la disponibilité des matériaux, les programmes CN, l’outillage (y compris la durée de vie restante des outils), les montages, etc. Ce n’est que lorsque tout est prêt que le système lance la production. Par conséquent, nous avons beaucoup moins de pièces en attente entre les opérations”.
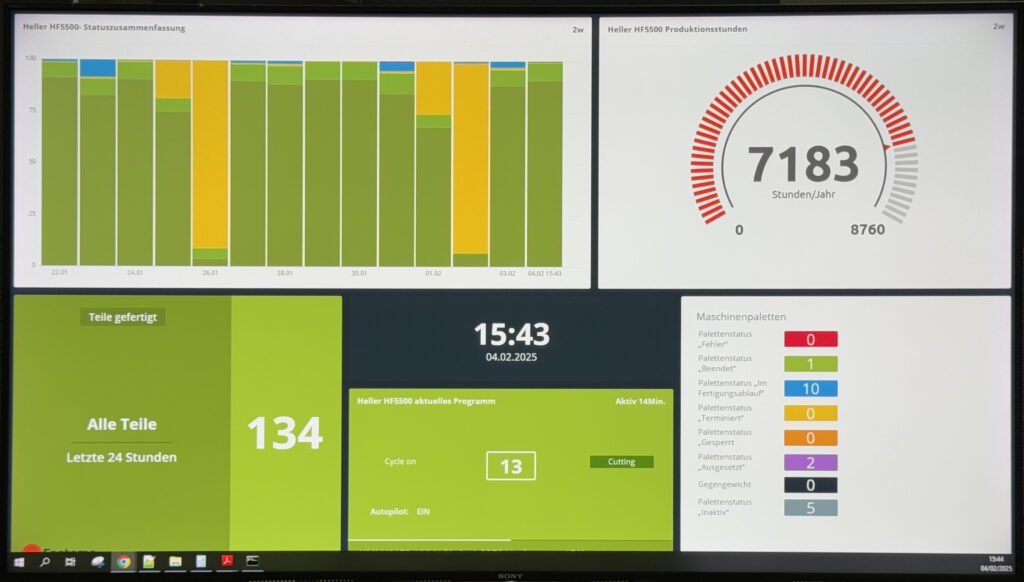
Gestion centralisée des ressources de production
Une fois que les données relatives aux pièces sont stockées dans le SGM, les commandes répétitives peuvent être lancées immédiatement. “Cela nous permet de gagner énormément de temps, à condition que les matières premières, les palettes et les outils soient prêts”, explique M. Fischer. “Le MMS prend également en charge la gestion complète des outils et envoie des instructions à l’unité de préréglage. De cette manière, toutes nos ressources de production critiques sont gérées de manière centralisée.
Il ajoute : “Oui, les logiciels ne coupent pas le métal, mais ils augmentent considérablement les heures de broche : “Oui, les logiciels ne coupent pas le métal, mais ils augmentent considérablement le nombre d’heures de broche. Chaque minute pendant laquelle une machine ne fabrique pas de copeaux est du gaspillage”. Actuellement, les ordres de production sont encore saisis manuellement dans le système de contrôle. Mais avec l’intégration future de MMS dans le système ERP, les 20 employés de l’équipe F1 acquièrent déjà une expérience pratique précieuse du logiciel et de son potentiel.
Le flux de pièces avec le FPT-1000
Aujourd’hui, le FPT-1000 de Cutmetall contient 18 palettes de différentes hauteurs. Les montages restent sur les palettes de la machine et chaque palette contient généralement un seul type de pièce. Après l’OP10, les pièces sont de nouveau serrées sur la même palette pour l’OP20.
“Lorsqu’une palette revient du FPT, nous avons toujours un mélange de pièces finies, de pièces brutes prêtes pour l’OP10 et de pièces serrées pour l’OP20”, explique M. Fischer. “Les temps d’usinage des palettes varient entre 30 et 90 minutes.
L’installation fonctionne en deux équipes par jour, avec une équipe de nuit supplémentaire sans personnel. Pour ce faire, Cutmetall prévoit de transférer automatiquement les copeaux de toutes les machines vers un conteneur central.
Des résultats solides, des prochaines étapes claires
Avec le projet F1, Cutmetall a déjà atteint ses objectifs initiaux : acquérir une expérience pratique de l’automatisation, développer des connaissances internes et se préparer pour le niveau suivant.
Grâce à la solution FPT-1000, l’entreprise atteint désormais plus de 7 000 heures d’automatisation par an – dont 90 % sont des heures de broche proprement dites, et seulement 10 % utilisées pour les changements de palettes et d’outils.
“Pour une entreprise de taille moyenne comme la nôtre, dont les lots sont relativement petits, les investissements importants doivent être rentabilisés. Le fait que nous puissions désormais amortir une machine sur plus de 7 000 heures de production par an est une grande réussite.”